Send us your project information and our Sales & Engineering team will be in touch with you the same day.
Request A Quote
Low Pressure Die Casting
Often unknown or confused with a permanent mold process, Low Pressure Die Casting offers many advantages to other casting processes including superior metal quality, low tooling costs, excellent surface finish, and good as-cast tolerance capabilities. It is an excellent fit for parts of larger size and/or higher complexity. Of all available casting processes Low Pressure Die Casting produces the highest metal quality available in large part due to its bottom pull, bottom feed injection process. The holding furnace for the molten metal is located beneath the die/mold. Applying a pressure of up to 1 bar molten metal is fed from the base of the crucible up through a feeder tube and into the bottom of the die chamber. The die is permanent and typically made of nodular iron, although sand molds as well as cores are also possible. Molten metal fills the die from bottom to top making a pooling type fill which is laminar in nature. The upper portion of the “molten pool” is then pressed out through a catch and trimmed off making metal quality in the casting itself of very high quality. The upward movement of the molten metal is against gravity and after filling the die pressure from the crucible is maintained until complete solidification of the casting. As the molten metal shifts phases from liquid to solid and shrinks in size this ongoing pressure allows ample feed metal to be introduced countering any volume deficits or shrinkage porosity which would otherwise exist.
Advantages
- Very good metal quality
- Complex geometries possible as sand cores can be used
- Higher material utilization, no need for feeders
- High dimensional accuracy
- Cost effective for lower quantities
- Lower upfront tooling cost when compared to High Pressure Die Casting
- Cost effective for parts exceeding 12” in any given dimension
Disadvantages
- Slower casting cycles translates into a high per unit cost than High Pressure Die Casting
- Minimum wall thickness is not as thin as High Pressure Die Casting
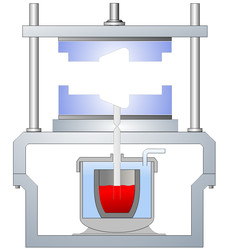
Low Pressure Die Casting Tooling
Tooling is typically a nodular iron permanent mold, although sand molds are also possible. Sand cores can also be utilized to achieve interior geometries that are not accessible by high-pressure die casting slides. Production low pressure die cast parts have highly repeatable properties and tolerances.
- Tooling = 4 weeks
- Samples = 1-2 weeks
- Production (Qty 1K) = 3-4 weeks
- 100k shots
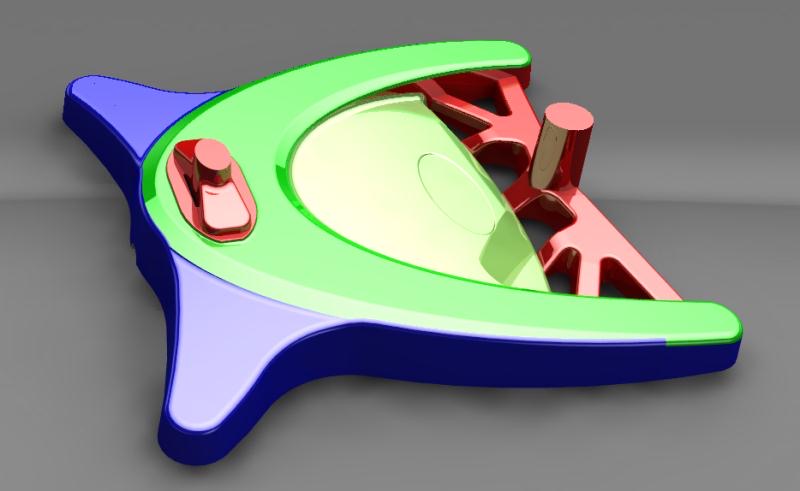
Materials
We pour a broad range of non-ferrous materials for low pressure die casting. The following are some of the most common alloys being used:
- Aluminum die casting alloys: A380, A356, A360 / ZL104, and K-Alloy
Design Criteria
- Standard tolerance of +/- .010” for the first inch and +/-.003” each additional inch.
- Typical surface finish of Ra 125 micro-inch as cast, post machining available for higher quality finishes.
- Minimum draft = .5 degrees
- Minimum wall thickness = .18” (Thinner wall thickness possible with alternative processes)
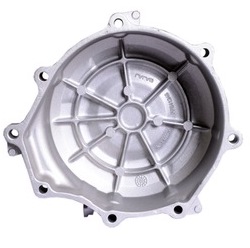
Low Pressure vs. High Pressure Die Casting
Preferred Vendor For
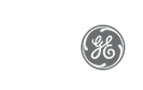
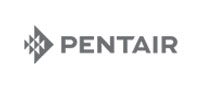

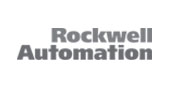
