Send us your project information and our Sales & Engineering team will be in touch with you the same day.
Request A Quote
Die Casting
Spectron Manufacturing is a leading die casting company, providing precision tooling and zinc and aluminum die castings. Die casting is a versatile process for producing engineered metal parts by forcing molten metal under high pressure into reusable steel molds. These molds, called dies, can be designed to produce complex shapes with a high degree of accuracy and repeatability. Parts can be sharply defined, with smooth or textured surfaces, and are suitable for a wide variety of attractive and serviceable finishes.
Our team of Machine Operators, Process Control Technicians, and Quality Personnel all work together to ensure our casting machine output meets or exceeds industry standards and customer specifications. We also perform a variety of secondary operations such as sanding, milling, drilling, tapping and assembly; as well as working with several top notch commercial painters. View all Secondary Operations capabilities.
Tooling Operations
Spectron manufactures prototype, low volume, and production die cast tooling. Our experienced, skilled team of CAD/CAM engineers and tooling professionals deliver quality tooling solutions for today’s demanding manufacturing environment.
Production Tooling
Hard tool or H-13 die cast tooling is an excellent process for higher quantity requirements. A larger upfront tooling investment yields a significant reduction in re-occurring costs. Production die cast parts have highly repeatable properties and tolerances.
- Tooling = 4 weeks
- Samples = 1-2 weeks
- Production (Qty 10k) = 3-4 weeks
- 150k shots
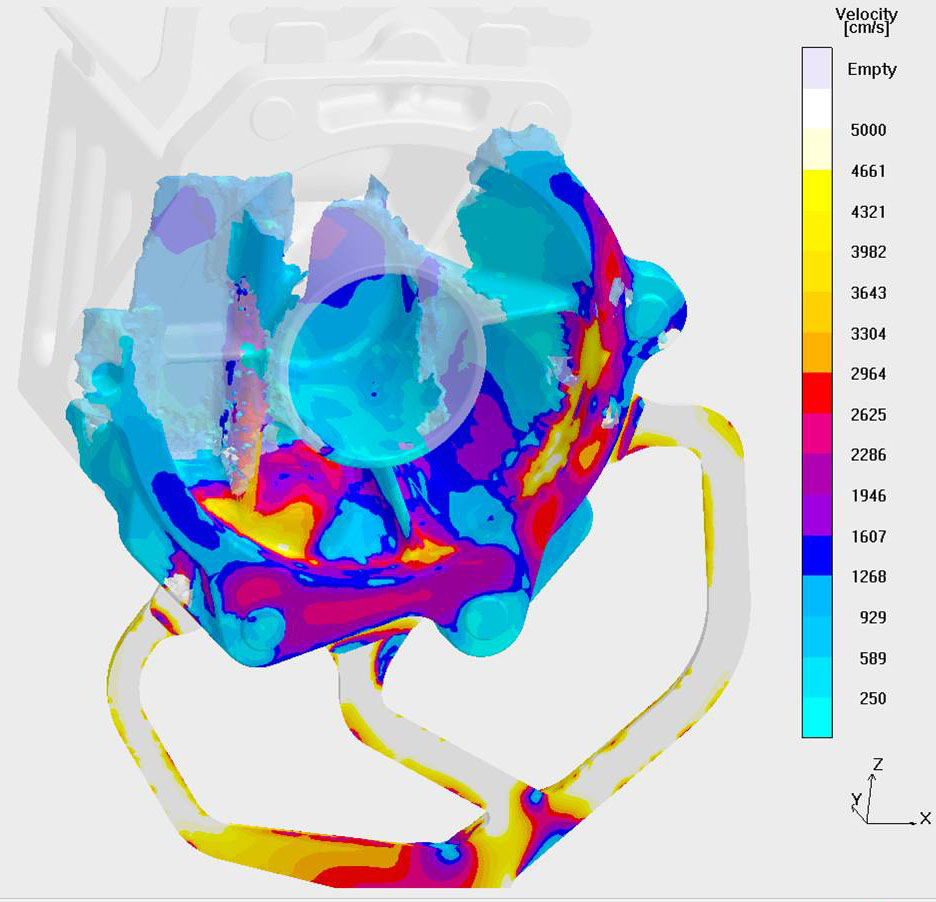
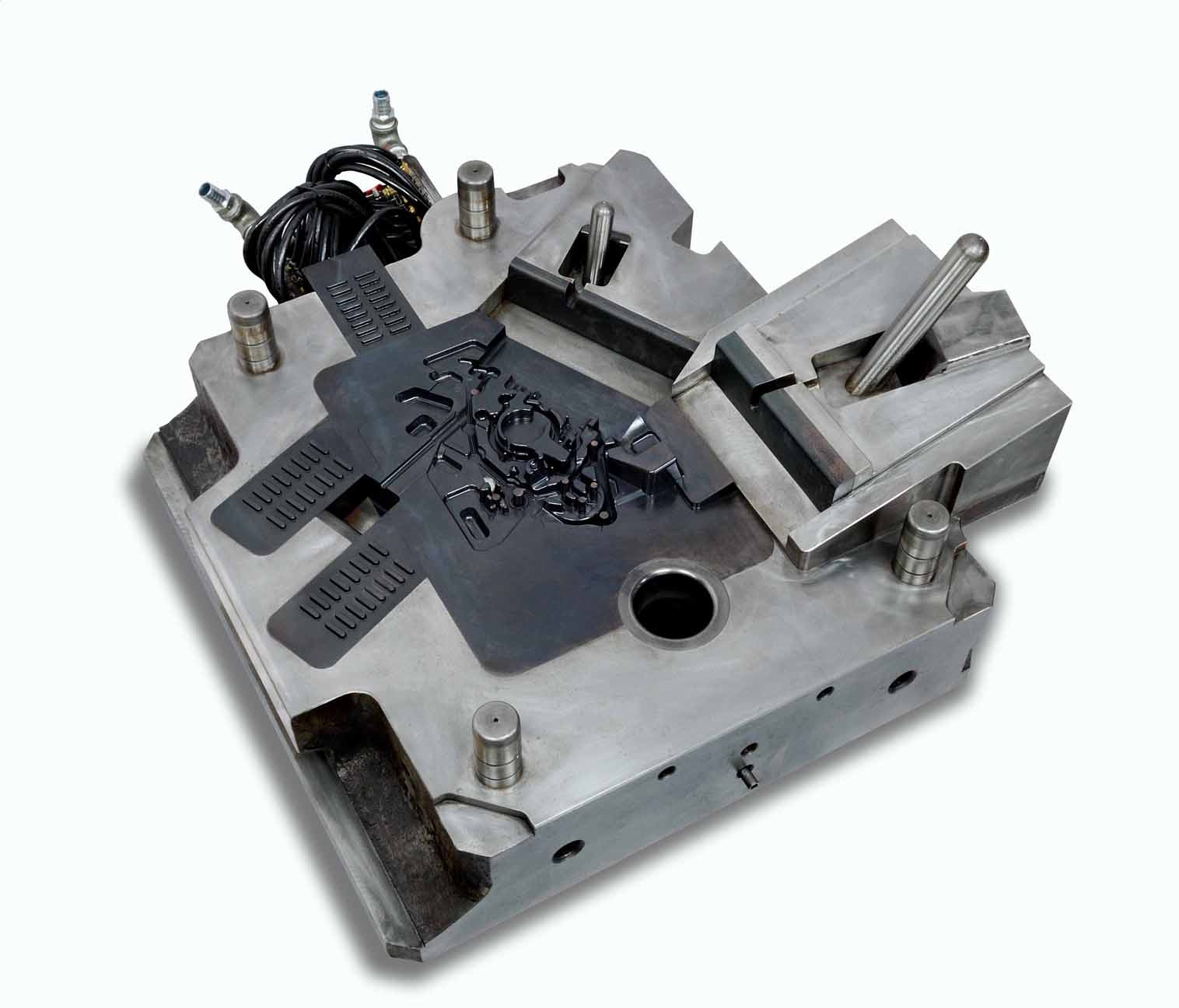
Prototype Tooling
The term “Soft Tool” is used to describe a die cast tool made out of P-20 steel. The P-20 steel is softer than H-13 steel and thus yields parts in less time with a decrease in tooling cost attributed to the ability to run faster feed rates when CNC machining the tool. Typically a P-20 tool can yield 10,000-40,000 parts before showing any significant wear.
- Tooling = 2 weeks
- Samples = 1-2 weeks
- Production (Qty 100) = 3-5 days
- 10k shots
Materials
We routinely pour a broad range of non-ferrous materials. The following are some of the most common alloys being used:
- Aluminum die casting alloys: A380, A356, A360, and K-Alloy
- Zinc die casting alloys include ZA8, ZA27, and Zamak 1 through Zamak 5
Design Criteria
- As cast tolerance as tight as +/- .005”, post machining available for tighter tolerance applications.
- Standard tolerance of +/- .005” for the first inch and +/-.002” each additional inch.
- Typical surface finish of Ra 63 micro-inch as cast, post machining available for higher quality finishes.
- Minimum draft = .5 degrees
- Zinc minimum wall thickness = .04”
- Aluminum minimum wall thickness = .08”
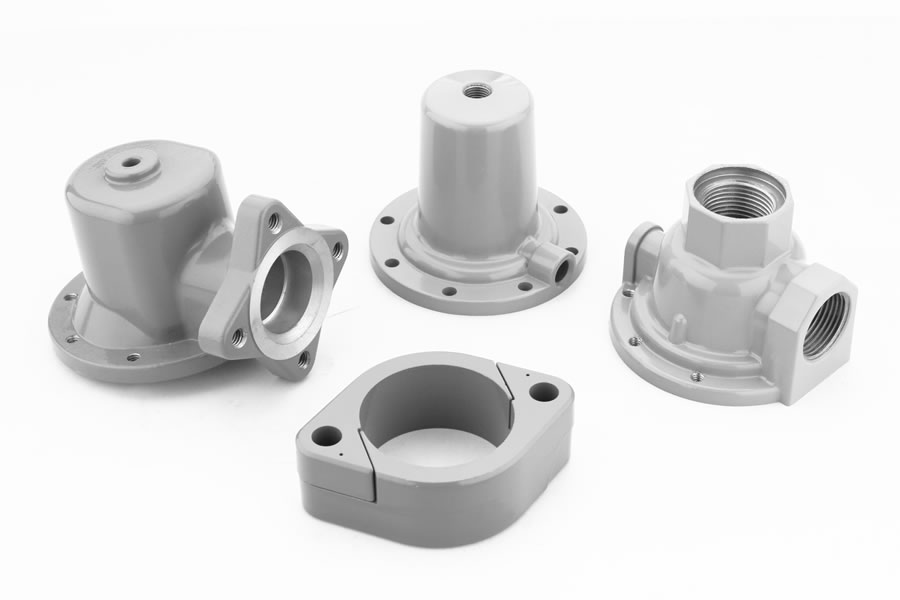
What our customers say
“Without Spectron our project would not have been as successful as it was. They demonstrated the teamwork, knowledge, and ‘can-do’ attitude needed to pull off a difficult order.”
Preferred Vendor For
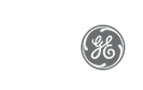
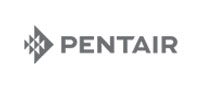

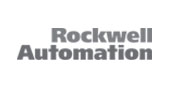
